|
 |
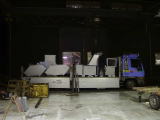 |
2007.12.03(月)
11月28日と同じく丸後運輸の社長が運転して来た。
前回積んだダクトが届いていないと問い合わせがあり、どっか崖にでも落ちているのでは?と噂されていたのだが・・・
Mission complete. |
|
 |
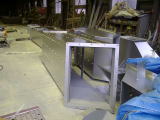 |
2007.12.01(土)
内貼の鉄板は間にゴム、それも高価なネオプレンゴムを挟むという豪華版。 |
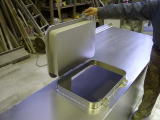 |
点検口は椿バルクシステムが独壇場のワンタッチ窓。
図面では残留防止タイプだったが、カタログにはあっても現物は市場にないので標準品を改造した。
厚みを持たせるため蓋の裏側につけた弁当ガラみたいなのがそれ。
溶接してないように見えるが、内側を全溶接してから蓋をかぶせた。
シュートの厚みにあわせて4.5mmの板を使ったこれも豪華版といえば豪華版。
実は4.5mmの残材はコマツのコンベアフレームを手がけている関係で腐るほどある。 |
|
 |
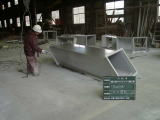 |
2007.11.30(金)
やっぱり工程写真は念のため、撮っておくことにした。
仕上塗装中。 |
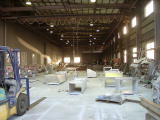 |
もうあとちょい。
月曜日の積み込みだから十分間に合う。 |
|
 |
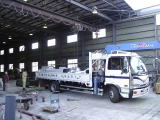 |
2007.11.29(木)
現場監督じきじき引き取りに現れた。
というか、シュートがどこまでできているか確認に来られたようだ。
ついでだから、とダクトの残りと、錆止を塗ってまだ仕上塗装の終わってないシュートを引き取っていった。 |
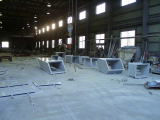 |
残りはあと、これらとまだ製作中のいくつか。
四トン車一台で乗るだろう。 |
|
 |
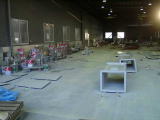 |
2007.11.28(水)
一部錆止塗装に取り掛かった。
工程写真はいらないのかな? |
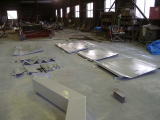 |
四面ばらばらにしたホッパー。
手順前後のため、ばらばらにしないと現場に入らなくなったのだろう。 |
 |
φ500のダクトが先にいる、と無理やり調達したと言う四トン車が引き取りに来た。
トラックはあっても運転手がいなくて、やむを得ず丸後運輸の社長が運転していくのだそうだ。(^^;)
10トン車が来れば全部片付いたのだが、また少し残ってしまった。 |
|
 |
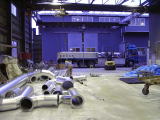 |
2007.11.27(火)
今日の出荷ですっきり片付くかと思ったら、な〜にがなにが。
丸いのでコロコロと積みようがなく、半分残ってしまった。 |
 |
シュートやホッパーの製作は続く。 |
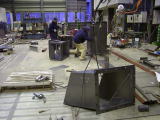 |
ダクトは断面が丸いのが多いが、シュートはたいがい四角。
丸いと底の一部分だけ磨耗する欠点がある。 |
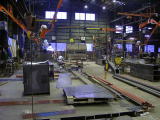 |
何を作っているのか調べる気も起こらない。
早く終わらせないと現場もさることながら、こっちの尻にも火が付いてしまう。 |
|
 |
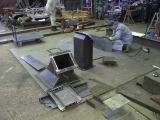 |
2007.11.26(月)
ぽつぽつと形になり始めた。
ダクトとどこが違うかと言うと、ダクトは気体が通り、シュートは粉体、粒体が通る。
形は似たようなもの。 |
 |
ややこしい格好をしているな。 |
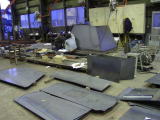 |
手前のほうにはまだ切ったままの材料がたくさん残っている。 |
|
 |
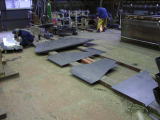 |
2007.11.24(土)
早く早くとせかされてもまだ板が切れたばかり。 |
|
 |
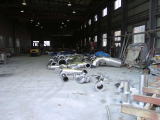 |
2007.11.20(火)
一日中不在だったので荷姿は見ることができなかった。
大型トラック一台分出荷したあと。
もうあと一台で乗せきれるかな。
シュートが追加されたのでまだまだ続くことになった。 |
|
 |
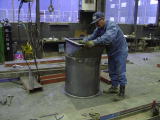 |
2007.11.12(月)
これは作り忘れ出はなく、追加のダクト。
これでダクトは塗装を除いて全部終わり |
|
 |
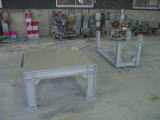 |
2007.11.10(土)
裏返っているのは排風機の架台。
手前の四角いのはサイレンサーの架台。 |
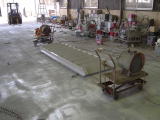 |
今日の夕方出荷なので錆止を塗ったあと送風機で風を送って乾かしている階段。 |
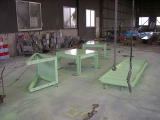 |
なんとか仕上塗装までこぎつけた。 |
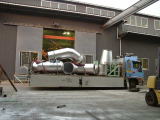 |
手すりは仕上塗装が間に合わなかった。
どうせ緑色かどうかはわからないし、現場で塗ってもらおう。
ダクトは急がないのだが、荷物が寂しいのでおまけ。 |
|
 |
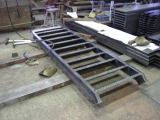 |
2007.11.09(金)
階段ができた。
右上に山のように積んであるのはコマツ向けBR380JG-1のフレーム材料。 |
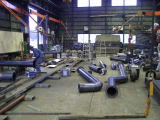 |
作り忘れのダクトはこの状態。 |
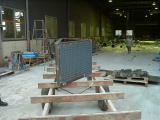 |
階段の踊場もできた。 |
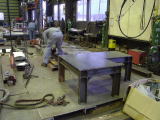 |
排風機(送風機と変わらない)の架台。
これがないと機械の据付ができず、ダクトの取付以前の問題なんだそうだ。 |
|
 |
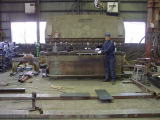 |
2007.11.08(木)
追加になった階段の踏み板を曲げている。 |
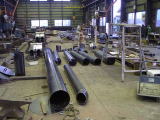 |
それより問題は図面が二枚抜け落ちていたことが判明、泡食って作っている。 |
|
 |
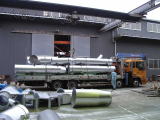 |
2007.11.06(火)
出荷第一陣はサポートの上にダクトを二段積み。
軽いけど、このぐらいが限界。 |
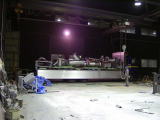 |
二号車を積み終わったのはもうとっぷり暮れた18時ごろ。
形が悪いので二段にも積めない。 |
|
 |
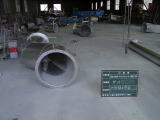 |
2007.11.05(月)
出荷は明日だと言うのに、φ500以上は内部も錆止を塗って欲しいという依頼が来た。
念のため黒板を入れて写真を撮っておく。 |
|
 |
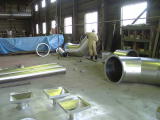 |
2007.11.02(金)
客先の検査があった。
特にほめられもせず、けなされもせず。(^^;) |
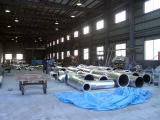 |
一回目の出荷分を並べたが、これが一台に乗るのかな。 |
|
 |
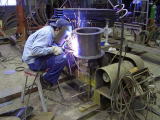 |
2007.11.01(木)
ダンパーのフランジ溶接はちょっと一工夫。
ターンテーブルがあればいいんだが、ないものねだりなので、ターニングロールを利用して回している。 |
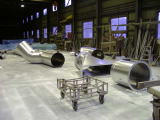 |
ひねりを加えたダクトと大きな角丸ができた。 |
|
 |
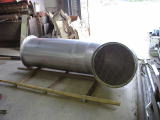 |
2007.10.31(水)
ステンレスダクトは外気に開放するので鳥が入ってこないように金網を張る。
これは線径が太い場合に使われるクリンプ金網と言うタイプ。
こうなると工程写真は無理だな。 |
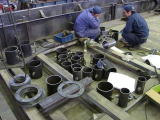 |
ダンパーの製作で思案中。 |
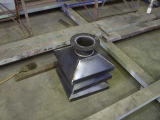 |
吸気口のフード、というかこれが吸気口そのもの。
角丸と言えないこともない。 |
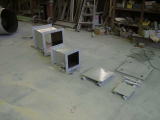 |
角ダクトのダンパー。
右のほうがダンパーの羽根。 |
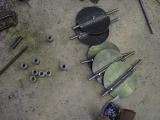 |
これは丸ダクトのダンパーの羽根。 |
|
 |
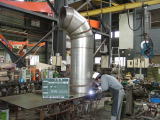 |
2007.10.30(火)
ステンレスダクトはTIG溶接。
溶接部は変色するので、あとで酸洗いしてきれいにする。 |
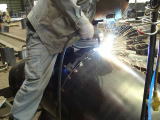 |
手振れしないように自在の定規を使っている。
新アイデアだけど、うまくいってるのかな? |
 |
今日の出来上がり。 |
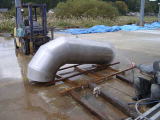 |
ありゃ。写真を撮る前に酸洗いが終わってる。
工程写真はどうしてくれる。 |
|
 |
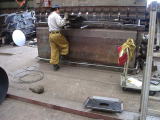 |
2007.10.29(月)
吸気口のフードを作っている。
集塵というより、臭気をとるつもりらしい。 |
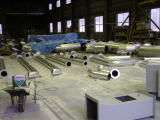 |
SGPで作ったダクトもぼちぼちと仕上塗装。 |
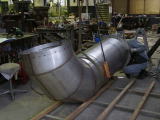 |
ステンレスダクトももうすぐできるが、これも黒板を入れて工程写真を撮っておいたほうがよさそうだな。
明日にしよう。 |
|
 |
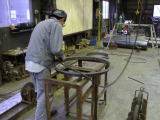 |
2007.10.27(土)
現場で位置決めするフランジはアングルを使うことになっている。
しかしアングルだと正確に穴を開けるのが大変なので、鉄板フランジに平鋼を溶接してアングル状にすることにした。 |
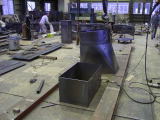 |
サイクロンの入口ダクト。
サイクロンは仕様が決まればすぐに設計はできるので、どっかで作ってもう現場に据え付いているのだろう。
サイクロンも作りたいか、と問われるとちょっとびみょ〜かな? (^^;) |
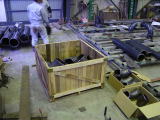 |
SGPのエルボがまだこんなに残っている。
あとはこまごまと曲がるめんどくさいダクトばかり残ったようだ。 |
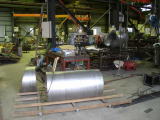 |
屋外に出る部分だけステンレスを使用する。
見積から落ちていて自腹を切った。(T_T) |
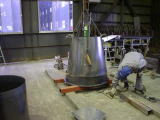 |
サイクロン出口ダクトが一番径が大きいφ1,050だが、長さはほんの200mmほど。 |
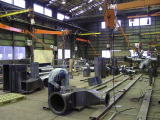 |
角ダクトの本付溶接。 |
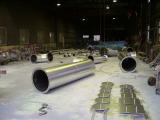 |
仕上塗装が終わったダクト。 |
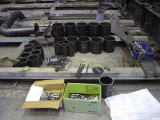 |
ダンパーの材料。
けっこうめんどくさい。 |
|
 |
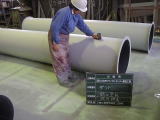 |
2007.10.26(金)
仕上塗装をする前に膜厚を測っておく。 |
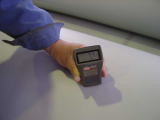 |
錆止一回、仕上げ一回で60μはちょっと厳しいので、錆止は二回塗って膜厚を稼いでおく。
ここでは77μあるが、薄いところでは50μほど。
仕上げであと20μぐらいはつくだろう。 |
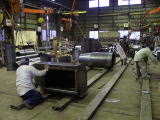 |
塗装にだいぶ回ったので、工場内はすこしすかすかして来た。 |
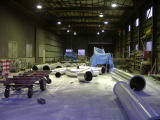 |
11月5日収めの分は仕上げまで来た。
少しでも早いほうがいいという話だったので、来週半ばには出荷する。 |
|
 |
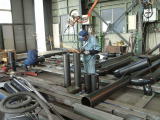 |
2007.10.25(木)
SGPは肉厚があるので、少し面を落としておいたほうがきれいに溶接できる。 |
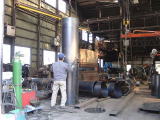 |
直管ダクトは立ててつないで仮止めする。 |
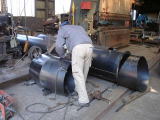 |
海老の部分は立てられないので自重が期待できず、レバーブロックなどで引っ張らなければならない。 |
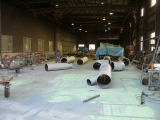 |
一番早い納期のダクトは錆止までこぎつけた。 |
|
 |
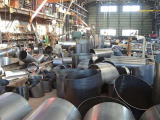 |
2007.10.24(水)
ダクトの海。
工場を横切るのも楽じゃない。
出来上がりの日程を知らせよと言われているけど、皆目見当もつかない。(-_-;) |
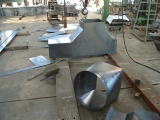 |
向こう側は角ダクトの分岐部分。
手前が角丸ダクト。
二十年前にBASICで書いた角丸ダクトの展開プログラムは超大作だった。
CADに連動する安い展開プログラムが手に入るまで、ほんの三、四年前までは現用していた。
今回から角丸の溶接部分はお客さんの薦めもあって四角のかどをめがけてやってみることにした。
見掛けは悪いが、材料の歩留まりはいいし、作りやすいみたいだ。 |
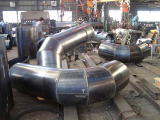 |
海老だらけ。
昔は瓦工場やレンガ工場でけっこうダクトの需要はあったが、近頃は窯業そのものが衰退してしまった。
地元のゴミ焼却場もなくなってしまったし・・・・
しかし切断が精密になったので海老など、宴たけなわだった昔よりかえってきれいにできている。
個人の技量は往年の職人技にはかなわないが、進歩した道具が補っている。 |
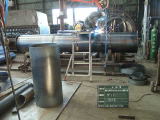 |
直管ダクトを接続して円周を溶接している。
インバータと言うのができて、簡単に普通の誘導モータの速度制御ができるようになった。
自作したときはあんなに手間が掛かったのに、今は同等の性能が数千円で手に入る。
というほど手間は掛かっていないのだが、売ってないので故障すると自分で直さなければならないのが欠点。(^^;) |
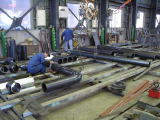 |
SGPを使った細いダクトの製作。
既製品のエルボは滑らかに曲がっている。 |
|
 |
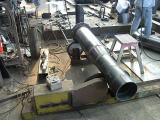 |
2007.10.23(火
ダクトとダクトをつないで溶接するときはターニング・ロールで回す。
インバータと言う普通の三相モータが使える便利な周波数変換器ができる前に自作した。
速度制御するときは直流モータを使うよりほかなく、電流制御はサイリスタによる。
サイリスタは何度か飛ばしたので、今は手持ちのトライアックを代用してある。
トライアックは交流用で、調光器なんかに使ってあるので、小さいものは家庭にも使われている。
トライアックで交流モータを制御してみたけど、使い物にならなかった。 |
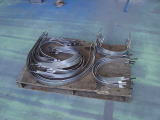 |
ダクトを押さえるバンド。
φ250(正確には267.4)以下はSGP用のUボルトが市販されているのでそれを使う。 |
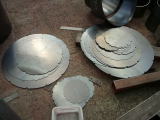 |
海老をつなぐときに断面を丸くするために作ったようだが、ぎざぎざがたくさんついているわけはなんだろう。
溶接ビードを逃がすためならひとつでいいはずだが。 |
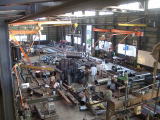 |
足の踏み場もなくなったが、今日になって優先順位が変更になった。
ミッドウェイ海戦みたく、土壇場になっても攻撃目標が定まらず、爆弾だ魚雷だ、と積み替えているようではすでに負け戦か。 |
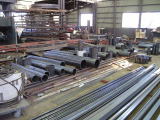 |
SGPの切断はほぼ終わったようだ。 |
|
 |
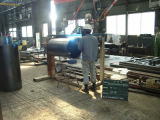 |
2007.10.22(月)
優先順位と納期が決まった。最初の納品は11月5日と延期になって一安心。
直管部分の縦方向継ぎ目溶接の様子。 |
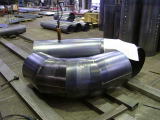 |
これが海老の腰と称するエルボダクト。
俗称エルボはelbowでひじのこと。
思えばエルボとレジューサと角丸の展開を計算でなんとかならんもんかとパソコンを始めたんだった。しみじみ・・・・
以前は原寸を書いて、図上で長さを測って鉄板に転記していた。
毎度毎度いちいち原寸を起こすのはσ(^_^)の役目だった。 |
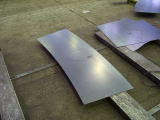 |
径が変わる部分、レジューサ・ダクトの板取は扇型。
パソコンの使い始めのころはプリンターが高くて買えないので、ディスプレイに表示される数字を紙に書き写していた。
NECのPC8801(無印)を使い、N88BASICでしこしこプログラムを書いた。
デバッグのためのプログラムリストもプリンターがないので手書きだった。(^^;) |
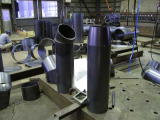 |
レジューサはこんな風になる。(立っているダクトの右のほう) |
|
 |
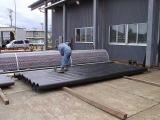 |
2007.10.20(土)
φ250以下はSGP(ガス管)を使用する。
防錆油が塗ってあって、このままでは触れば真っ黒になるし、塗装もできないのでシンナーでふき取る。 |
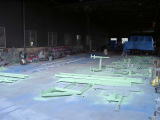 |
ありゃりゃ。
写真を撮らないうちに仕上塗装にまで進んでる。 |
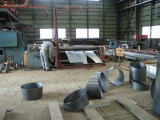 |
海老部分の曲げ。
まだ形がわからないが、出来上がった製品を見ると、なるほど海老に見えると思う。 |
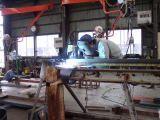 |
直線部分は短くてもなるべくすみっこ君を使う。
ビードの整形をいかに少なくするかが採算の鍵。
薄板の溶接はどうしてもミミズが這ったような溶接になってしまい、ディスクグラインダーで削る時間のほうが長くなる。 |
|
 |
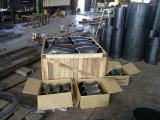 |
2007.10.18(木)
細いダクトに使用する溶接エルボが入荷した。
150Aは標準在庫なのか、ダンボールに三つずつ入っている。 |
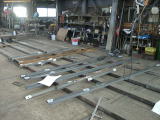 |
白いところは番号を書いておくために先に錆止を塗った。
番号を書いたらガムテープで塗料がつかないよう隠しておく。 |
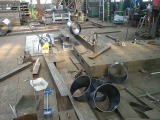 |
海老(エルボダクト)の部分も作り始めた。 |
|
 |
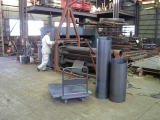 |
2007.10.17(水)
ダクトを巻き始めた。 |
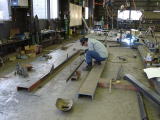 |
平行してサポートを製作する。 |
|
 |
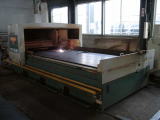 |
2007.10.16(火)
やっとフランジから切断を開始した。 |
|
 |
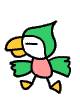 |
2007.10.11(木)
材料を注文した。 |
|
 |
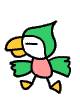 |
2007.10.05(金)
黒板が届いた。 |
|
 |
 |
2007.10.02(火)
正式に発注されたが、ダクトは正直あんまりうれしくない。
薄板の突合せ溶接はどうしても見掛けが汚くなる。
グラインダーで化粧直しをしなくていいように溶接できれば何とか採算に乗るのだが。 |
|
 |